آنچه در این مقاله میخوانید:
تولید ورق از شمش فولادی
یکی از قابلیتهای مهم و استراتژیک هر کشوری در حوزه صنعت میزان تولید فولاد و ورق فولادی میباشد. از آن جا که ایران یکی از کشورهای غنی از معادن سنگ آهن است، دسترسی به مواد اولیه تولید فولاد در این کشور آسان است و با توجه به سرمایهگذاری انجام شده در صنعت فولاد، این کشور به عنوان یکی از تولیدکنندگان فولاد و ورقهای فولادی در سطح دنیا شناخته میشود. بدون شک ورق فولادی به عنوان ماده اولیه اساسی و کاربردی در صنایع مختلف مورد استفاده قرار میگیرد که عدم تولید آن، میتواند توسعه و پیشرفت بسیاری از صنایع را با دشواری مواجه کند.
به طور کلی، انواع ورقهای فولادی با آلیاژهای متفاوت و به شکل رول یا برش خورده (شیت) تولید شده و به فروش میرسند. هر کدام از انواع ورقهای فولادی تولید شده از شمش فولادی، با توجه به ساختار و خواص معینی که دارند، کاربرد متفاوتی خواهند داشت. در این مقاله با ما همراه باشید تا با نحوه تولید و تبدیل شمش فولادی به ورق فولادی آشنا شوید.
ورقهای فولادی از نورد شمشهای فولادی تولید میشوند. قبل از معرفی انواع نورد، بهتر است کمی در خصوص نحوه تولید شمشهای فولادی صحبت کنیم.
تولید شمش فولاد
مراحل تولید شمشهای فولادی به شرح زیر میباشد:
استخراج سنگ آهن
اولین مرحله در تولید شمش فولادی، استخراج سنگ آهن از معادن است. در این مرحله با شناسایی سنگ آهن موجود در نواحی مختلف کشور اقدام به حفاری و تاسیس معدن میگردد که در ایران معادن گل گوهر، چادرملو، چغارت، سنگ لردگان، سنگان و غیره از جمله معادن سنگ آهن میباشند. پس از احداث معدن اقدام به استخراج سنگ آهن و ارسال آن به کارخانههای فرآوری آهن میگردد.
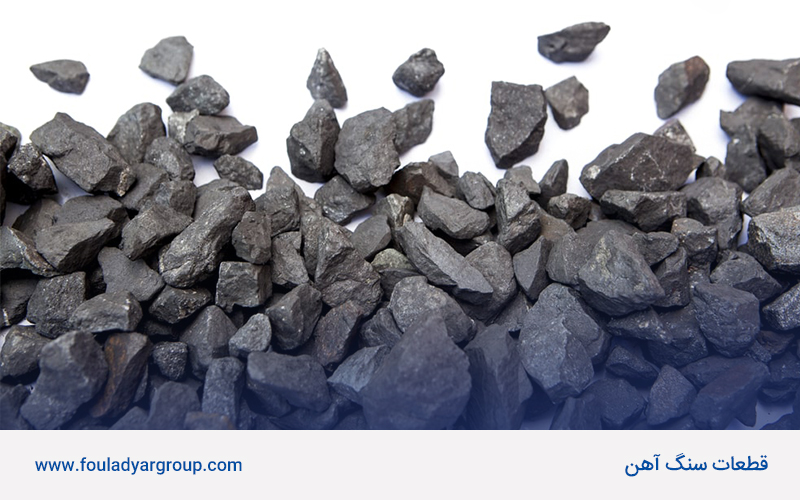
فرآوری سنگ آهن
دومین مرحله، فرآوری سنگ آهن میباشد که با هدف حذف ناخالصیهای موجود در سنگ آهن و تبدیل آن به اشکال گلولهای (گندلهسازی) صورت میپذیرد.
تولید آهن اسفنجی
تولید آهن اسفنجی بر اساس فرآیندهایی بر پایه گاز و یا برپایه ذغال سنگ صورت میپذیرد که هدف از این کار، جداسازی اکسیژن از ترکیب گندلههای آهن میباشد. خروجی این مرحله، تکههای متخلخلی به اسم آهن اسفنجی میباشد.
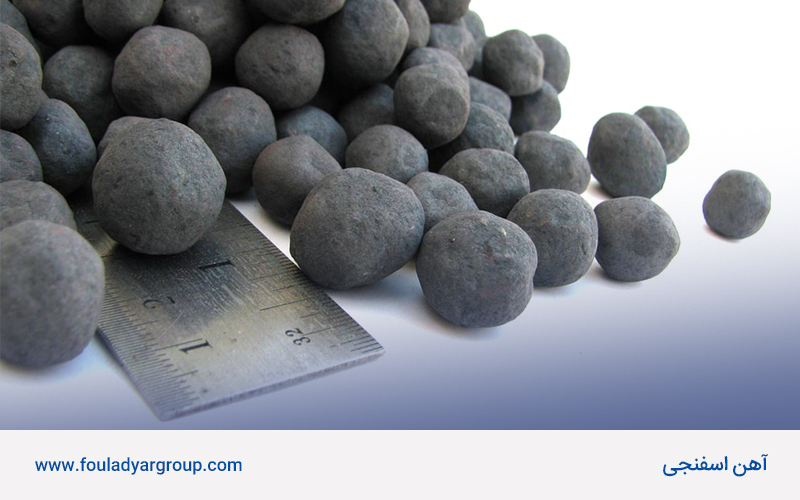
تولید شمش فولادی
در این مرحله با حرارت دادن آهن اسفنجی در کورههای ذوب آهن و فرآوری آن، شمشهای فولادی تولید میگردند که با تغییر شکل شمشهای فولادی میتوان محصولاتی نظیر بلوم، بیلت و اسلب تولید کرد که هرکدام از آنها برای تولید محصولات خاصی مورد استفاده قرار میگیرند. برای تولید ورقهای فولادی از اسلب (تختال) استفاده میشود.
تبدیل اسلب به ورق فولادی
همانطور که بیان شد برای تولید ورق فولادی میبایست شمشهای فولادی را به اسلب یا تختال تبدیل کرد تا بتوان به راحتی از طریق یکی از دو روش نورد گرم یا نورد سرد اسلبهای فولادی را به ورق فولادی تبدیل نمود.
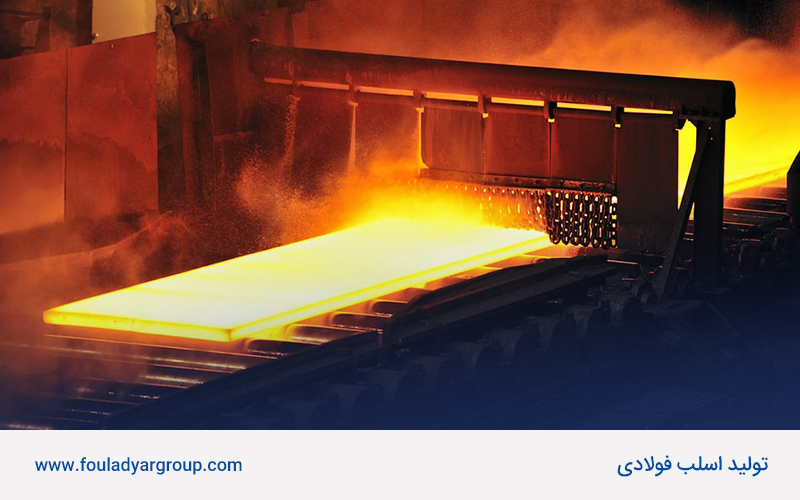
تولید ورق فولادی به روش نورد گرم
فرآیند نورد گرم برای تولید ورق فولادی به شرح زیر است:
کورههای پیشگرم
اسلبهای فولادی تولید شده، دارای طولی بین 6 تا ۱2 متر، ضخامتی بین 20۰ تا 25۰ میلیمتر و عرضی بین ۶5۰ تا ۲0۰۰ میلیمتر هستند. برای اینکه عملیات نورد گرم به راحتی انجام شود و به نوعی با اعمال فشار و نیروی کمتری، تختالهای فولادی نورد و نازکتر شوند، در کورههای پیشگرم شمشهای فولادی حرارت دهی میشوند. محدودهی دمایی کورههای پیش گرم برای حرارت دادن به شمشهای فولادی بیش از 1000 درجه سانتیگراد است.
عملیات پوستشکنی
مرحله بعدی تولید ورق فولادی عملیات پوستشکنی است. در عملیات پیشگرم، سطح روی اسلبها یا همان تختالهای فولادی بسیار داغ شده که به راحتی با اکسیژن هوا وارد واکنش شده و روی آنها پوسته پوستههایی ایجاد میشود. در این شرایط، طی عملیات ویژه با فشار آب بالا، پوستهها اکسید شده و از سطح شمشهای فولادی جدا میشوند.
پرسکاری با نورد دو یا چهار غلتکه
بعد از انجام پوستشکنی، نوبت به پرسکاری و به نوعی کاهش ضخامت و عرض اسلبهای فولادی میرسد. در این مرحله از تولید ورق فولادی، با استفاده از نورد چهار یا دو غلتکه، ضخامت تختالهای فولادی به ۲۰ تا ۶۰ میلیمتر میرسند. در حقیقت نیروی عمودی وارد شده به اسلبها از سوی غلتکها باعث میشود در حین عبور از میان آنها ضخامت اسلب کاهش پیدا کند و در نهایت ورق فولادی تولید شود.
پوستشکنی ثانویه و برشکاری
در این مرحله ورق تولیدی با چرخهای انتقال، به بخش برشکاری منتقل شده و بخشهای انتهایی و ابتدایی آن کاملا برش داده میشوند. سپس ورقهای برش داده شده به سمت پوستشکنی ثانویه هدایت میشوند. در این بخش دوباره با فشار آب بالا، پوستهای اکسید شده از روی سطح محصول برداشته میشوند.
نورد چهار یا هفت غلتکه
پس از پوستزدایی ثانویه، ورقها به بخش نورد پایانی برده میشوند. در این قسمت با استفاده از نورد چهار تا هفت غلتکه، میزان ضخامت ورق نازکتر میشود. به طور کلی در این مرحله، ضخامت بین 1.5 تا 20 میلیمتر خواهد شد و به نوعی به ورق فولادی با ضخامت استاندارد تبدیل میشود.
دستگاه خنککننده و بستهبندی
ورق فولادی برای خنک شدن وارد دستگاههای خنک کننده آبی میشود و دمای آن به ۵۰۰ تا ۷۰۰ درجه سانتی گراد میرسد. در مرحله آخر، ورق فولادی از خط نورد خارج شده و تبدیل به رول فولادی میگردد.
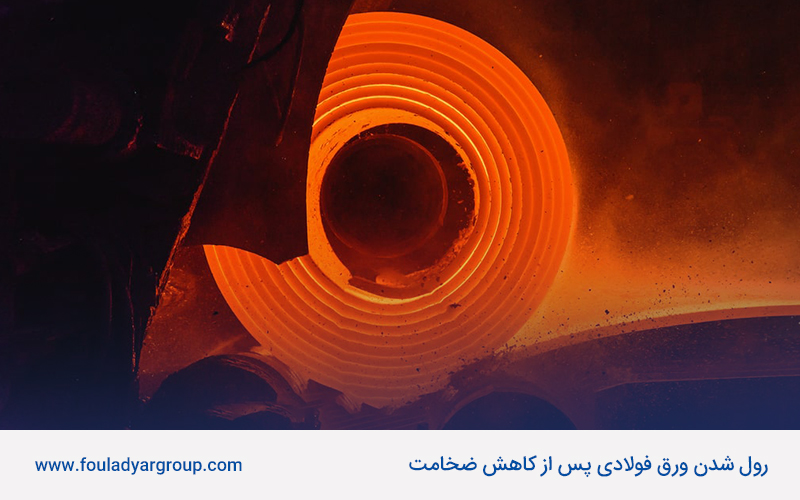
تولید ورق فولادی به شیوه نورد سرد
ورق فولادی تولید شده به روش گرم، سطح ناهمگن و ناصافی دارد و برای تولیدات برخی از محصولات صنعتی ایدهآل به نظر نمیرسد. در شیوه نورد سرد میتوان تا حد زیادی سطح ورق فولادی را صاف و صیقلی کرد و همچنین ضخامت آنها را نیز تا حدودی کمتر نمود. همچنین، ورقهای فولادی تولید شده به روش نورد گرم، به دلیل خواص مکانیکی پایینتر از استحکام کمتری برخودار هستند و استفاده از روش نورد سرد روی آنها تا حد زیادی استحکام این نوع ورقها را افزایش میدهد. فرایند نورد سرد برای تولید ورق فولادی اغلب در دمای اتاق انجام میشود که در این صورت، اکسید شدن سطح روی ورقها اتفاق نمیافتد. در نظر داشته باشید، برای تولید ورق به روش نورد سرد از ورقهای فولادی تولید شده به روش نورد گرم استفاده میشود که با توجه به این توضیحات میتوان گفت، فرآیند تولید ورق فولادی به روش نورد سرد، زمانبرتر است و مراحل آن بیشتر از مراحل تولید ورق فولادی به روش گرم خواهد بود. به طور کلی، مراحل تولید ورق فولادی به روش سرد، شامل موارد زیر است:
اسیدشویی
بعد از اتمام فرآیند نورد گرم و تولید ورق فولادی سیاه، این نوع ورقها که سطح ناصاف و کمی اکسیدشده دارند در محلولی اسیدی که معمولا اسید کلریدریک بوده، غوطهور خواهند شد که موجب صاف و صیقلی شدن سطح ورق میشود.
نورد غلتکی
بعد از اتمام فرآیند اسیدشویی، برای کاهش ضخامت ورقها، آنها را از نورد غلتکی عبور میدهند که این امر باعث کاهش ضخامت ورق به کمتر از یک میلیمتر نیز میشود. در نظر داشته باشید برای سرد شدن ورقها، روان نگهداشتن غلتکها و هچنین افزایش مقاومت سطح ورق در برابر اکسیژن و خوردگی، روغن به کار میرود، به همین دلیل به ورقهای سرد، ورق روغنی هم میگویند.
رنگ کاری و گالوانیزاسیون
سطح ورقهای سرد (روغنی) تولید شده با استفاده از مراحل تکمیلی نظیر ایجاد پوشش با زینک (روی) توسط فرآیندی به نام گالوانیزاسیون و یا ایجاد پوشش رنگی در برابر خوردگی، زنگزدگی مقاوم شده که به ورقهای فولادی گالوانیزه و ورقهای فولادی رنگی شناخته میشوند.
نتیجهگیری
با توجه به اهمیت تولید ورقهای فولادی در صنعت میبایست برای تولید این محصول در کشور با سرمایه گذاری در سطح کلان اقدام به راه اندازی معادن سنگ آهن، کارخانجات ذوب آهن برای تولید شمشهای فولادی و همچنین ایجاد کارخانجات نورد گرم و نورد سرد برای تولید ورقهای سیاه و روغنی نمود. که با توجه به ظرفیت بالای ایران در داشتن معادن آهن میتوان با ارتقا دانش فنی و استفاده از تکنولوژی روز دنیا در زنجیره تولید ورق فولادی از این فرصت استفاده نمود تا علاوه بر پاسخگویی به نیاز داخلی، اقدام به تولید محصولات با کیفیت بالا برای صادرات و رونق اقتصادی استفاده نمود.
همچنین تولید شمش فولادی به ورق فولادی با توجه به فرآیندها و عملیات نورد صورت گرفته بر روی شمش محصول نهایی ویژگیها و مشخصات خاص خود را دارا میباشد که براساس ضخامت و خواص مکانیکی مورد نظر میتوان از انواع ورقهای فولادی استفاده نمود.
برای مشاوره و خرید انواع ورق فولادی میتوانید از طریق تماس با شماره 02172125 با واحد فروش فولادیار کوروش ارتباط برقرار کنید.